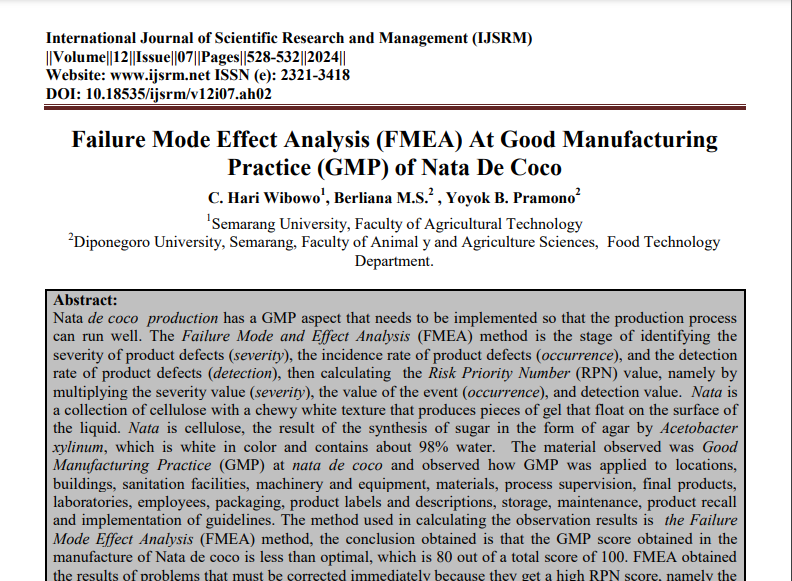
Submission to VIJ 2024-07-28
Keywords
- FMEA, nata de coco, GMP
Copyright (c) 2024 Cornelius Hari Wibowo, Yoyok Budi Pramono, Berliana M.S

This work is licensed under a Creative Commons Attribution 4.0 International License.
Abstract
Nata de coco production has a GMP aspect that needs to be implemented so that the production process can run well. The Failure Mode and Effect Analysis (FMEA) method is the stage of identifying the severity of product defects (severity), the incidence rate of product defects (occurrence), and the detection rate of product defects (detection), then calculating the Risk Priority Number (RPN) value, namely by multiplying the severity value (severity), the value of the event (occurrence), and detection value. Nata is a collection of cellulose with a chewy white texture that produces pieces of gel that float on the surface of the liquid. Nata is cellulose, the result of the synthesis of sugar in the form of agar by Acetobacter xylinum, which is white in color and contains about 98% water. The material observed was Good Manufacturing Practice (GMP) at nata de coco and observed how GMP was applied to locations, buildings, sanitation facilities, machinery and equipment, materials, process supervision, final products, laboratories, employees, packaging, product labels and descriptions, storage, maintenance, product recall and implementation of guidelines. The method used in calculating the observation results is the Failure Mode Effect Analysis (FMEA) method, the conclusion obtained is that the GMP score obtained in the manufacture of Nata de coco is less than optimal, which is 80 out of a total score of 100. FMEA obtained the results of problems that must be corrected immediately because they get a high RPN score, namely the pasteurization, cooling, drying, secondary packaging and storage of finished products Corrective actions and improvements need to be carried out immediately, especially in areas that receive high (critical) RPN scores, namely in the pasteurization, cooling, drying, secondary packaging and storage of finished products to avoid too many rejected products and product contamination. the lack of maximum GMP score can be identified as the source of the problem using the FMEA quantitative method. Failure Mode Effect Analysis (FMEA) is an effective tool in managing the potential for failure (failure mode), the results that arise from the failure mode and the level of criticality of the effect of the failure mode of the system of a product.
References
- Anastasya, A., dan Yuamita, F. 2022. Quality control in the production of drinking water in 330 ml bottles using the failure mode effect analysis (FMEA) method at PDAM Tirta Sembada. J. Teknologi dan Manajemen Industri Terapan. 1(I), 15-21
- Bastuti, S. 2020. Work accident risk analysis using failure mode and effect analysis (FMEA) and fault tree analysis (FTA) methods to reduce the level of work accident risk (PT. Blessing of Mirza Insani). J. Ilmiah dan Teknologi. 2(1): 48-52.
- Hamad, A., Handayani, N. A., dan Puspawiningtyas, E. 2014. Effect of Acetobacter xylinum starter age on nata de coco production. J. Techno Fakultas Teknik. 15(1): 37-49
- Kartikasari, V., dan Romadhon, H. 2019. Analysis of control and quality improvement of tuna canning process using failure mode and effect analysis (FMEA) and fault tree analysis (FTA) methods case study at PT XXX East Java. J. Pandangan Industri. 1(1): 1-10.
- Rini, F. A., Katili, P. B., dan Ummi, N. 2015. The application of Good Manufacturing Practices for the fulfillment of quality management in the production of bottled drinking water (Case Study at PT. XYZ). J. Teknik Industri Untirta. 3(2).
- Rizal, M., Jufriyanto, M., dan Rizqi, A. W. 2022. Work accident risk analysis using the failure mode and effect analysis (FMEA) method(Case Study: Project Economizer, Scrubber Tank and Draiyer Workers at PT. Petrokimia Gresik). J. Sains, Teknologi dan Industri. 20(1): 156-165.
- Sarinah, S., dan Djatna, T. 2015. Analysis of strategies for handling the risk of supply shortage in the seaweed processing industry: the case in South Sulawesi. J. Agritech. 35(2): 223-233.
- Utami, U., Harianie, L., Kusmiyati, N., dan Fitriasari, P. D. 2020. Training on making nata de coco at the PKK in Tasikmadu, Lowokwaru, Malang City. J. Pengabdian pada Masyarakat. 5(1): 149-156.